Introduction to LightForce Part 1: 3D-Printing the Next Generation of Fixed Appliances
Computer-assisted design and manufacturing (CAD/CAM) technology has changed the landscape of dentistry over the past few decades. Despite the rapid proliferation of CAD/CAM-produced clear aligners in recent years, however, traditional labial fixed appliances remain the most common form of orthodontic treatment around the world.
Most labial fixed appliance systems in use today follow a one-size-fits-all approach, with stock brackets mass-produced by analog manufacturing techniques such as injection molding. These systems apply the same prescription to every patient, without accounting for individual tooth anatomy or malocclusion type. The resulting undesirable or incomplete tooth movements may limit the clinician’s ability to achieve an ideal orthodontic outcome within a reasonable timeframe,1 and may require significant detailing adjustments that involve bracket repositioning, wirebending, or the addition of auxiliaries.
The deficiencies of standard brackets point to an obvious and timely opportunity for a comprehensive, fully customized fixed appliance solution. In response to this need, various CAD/CAM methods of customization have been introduced, including custom slot milling,2 robotic wirebending,3 and digital setup of analog brackets.4
Additive manufacturing represents the most recent evolution of CAD/CAM technology in orthodontics. By enabling complete customization of fixed appliances through 3D printing, this technology provides virtually infinite options for individualized treatment and offers an array of unique digital solutions to enhance clinical practice.
Why 3D Printing?
Three-dimensional printing is a well-suited manufacturing technique for fixed appliances because it excels at producing small, complex geometries at scale.5,6 The capability of fabricating digitally designed, 3D-printed brackets with anatomically unique bases and individualized prescriptions marks the beginning of a new generation of customized labial appliances (Fig. 1). The digital ecosystem of 3D printing also empowers clinicians to develop a fully digital workflow and virtual treatment plan for every fixed appliance patient.
Beyond the clinical benefits, 3D printing encourages the process of orthodontic product development. It facilitates dynamic product evolution, since hardware improvements (the printed objects) can change at the rapid pace of software development. New bracket features can be digitally designed, printed, tested, and clinically implemented within weeks. This stands in contrast to traditionally manufactured brackets, which require a significant investment of time and financial resources to update or change.
LightForce System
The first 3D-printed fixed appliance system was introduced in 2019 by LightForce Orthodontics.7 LightForce brackets are manufactured from 3D-printed polycrystalline alumina and are fully customized for all teeth, including the molars (Fig. 2). LightPlan cloud-based software enables individualized digital treatment planning: the virtual setup of the dentition in LightPlan results in a fully customized bracket prescription for each patient (Fig. 3). Other features of the system include a selection of three slot sizes (.018", .020", or .022"), as well as multiple bidimensional combinations, a choice of two color options (translucent or white), customizable digital bite turbos, and a precise indirect bonding system.
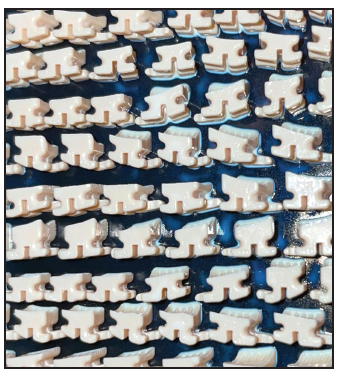
Fig. 1 LightForce* three-dimensionally printed brackets shown on printer build plate prior to processing.
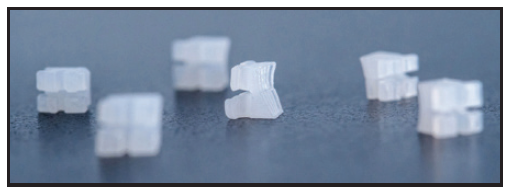
Fig. 2 LightForce brackets with anatomically unique custom bases manufactured from 3D-printed polycrystalline alumina.
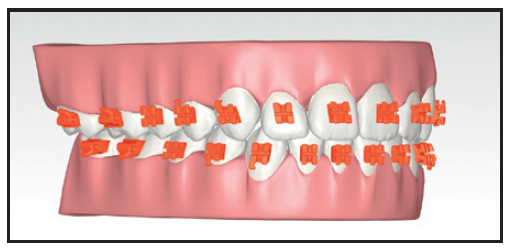
Fig. 3 LightPlan* cloud-based digital planning software provides customized bracket prescriptions.
The anatomical custom bases and dimensionally accurate slots of the LightForce system create an effective straightwire appliance. This distinguishes LightForce from previous customized systems, in which customization was primarily or partially achieved by means of robotically bent, patient-specific wires. Advantages of using fully customized brackets at the start of treatment (instead of generating custom finishing wires in the middle of treatment) include the accuracy of indirect bonding, the capacity to utilize a wider range of wires based on patient needs and treatment challenges, and the ability to envision the end result at the start of treatment. Additionally, it is more biologically sound and mechanically efficient to start with a customized bracket that moves the teeth consistently toward the intended positions, rather than allowing the initial bracket placement to move the teeth into unintended positions and then correcting those positions with customized wires at the end of treatment.
The LightForce digital workflow involves five steps:
- The orthodontic practice submits digital records, including an intraoral scan, photographs, radiographs, and the prescription form.
- The doctor reviews the initial LightPlan, edits the treatment plan as needed using full-3D controls, and approves the case for manufacturing.
- The 3D-printed custom brackets and indirect bonding trays are produced in LightForce’s manufacturing facility. Brackets are preloaded in the indirect bonding trays and sent to the orthodontic practice, ready for bonding (Fig. 4).
- Indirect bonding is performed at the chair.
- The clinician continues to manage the case.
LightPlan Setup
Based on the doctor’s submitted treatment goals and general clinical preferences, LightForce technicians create a virtual treatment plan that represents the desired treatment outcome. In reviewing the LightPlan, the doctor focuses on the positions of the teeth, so that the brackets will be designed by the software to achieve the intended tooth movements. In essence, the virtual setup becomes the individualized prescription for each patient.
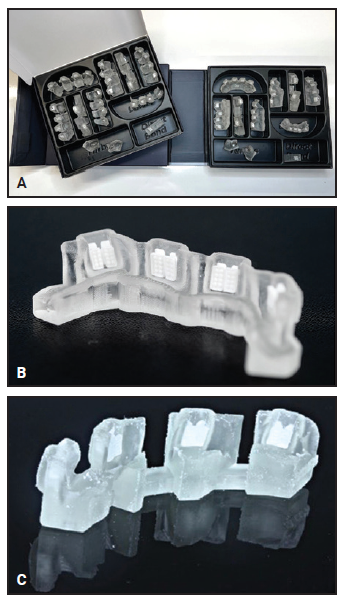
Fig. 4 A. Right: initial indirect bonding trays; left: single-tooth rebonding jigs. B. Close-up of indirect bonding tray sextant. C. Rebonding jigs, arranged in sextants, can be individually separated from their connections to precisely replace individual brackets at any point in treatment.
LightPlan is a robust clinical diagnostic and treatment-planning tool that allows detailed digital evaluation through such features as 3D tooth controls, superimposition, keyboard shortcuts, occlusal contacts, animation of proposed movements, grid views, Bolton analysis, and a Tooth Movement Table. In addition to the final occlusion and alignment, the doctor can customize other features, including the location and type of bracket hooks (Fig. 5).
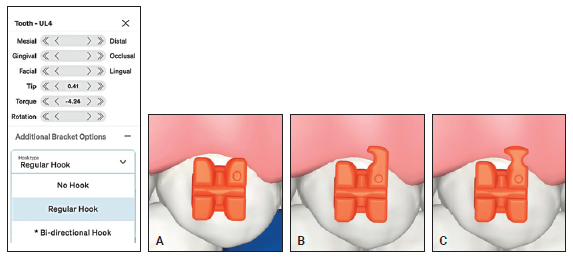
Fig. 5 Customizable LightPlan options for upper left first premolar include no hook (A), unidirectional hook (B), and bidirectional hook (C).
LightForce Brackets
LightForce 3D-printing technology provides several novel features:
1. The custom base fits perfectly on the labial surface of the tooth, even in the presence of a significant anatomical anomaly (Fig. 6). This capability ensures consistently accurate alignment with straight wires.
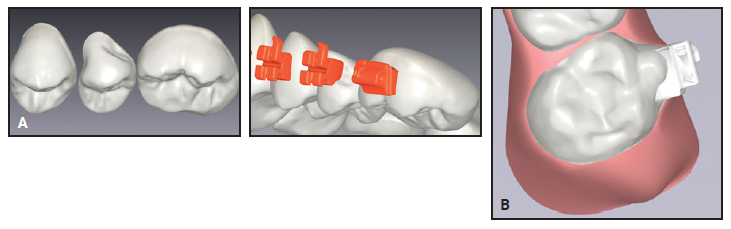
Fig. 6 A. Despite significant anatomical anomaly on upper left second premolar, custom bracket base adapts to maintain slot in straightwire configuration. B. Bracket adapts to anomalous anatomy of molar’s buccal cusp.
2. In contrast to conventional methods of edgewise bracket placement, the bracket need not be centered on the facial axis of the tooth, since any rotation can be compensated for by the custom anatomy of the bracket base. Therefore, almost any tooth can be bonded indirectly at the start of treatment, regardless of crowding or rotation (Fig. 7).
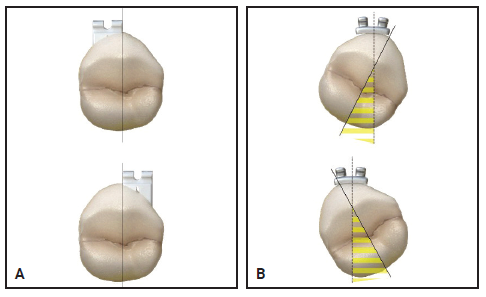
Fig. 7 A. LightForce custom base enables bracket placement on any portion of buccal surface. B. Same placement of standard bracket causes rotation.
3. Torque prescription is independent of vertical bracket position. This means the wire does not have to be positioned at the vertical midpoint of the clinical crown, as required with standard straight wires. The wire can be moved gingivally or occlusally according to such factors as the gingival margins or the occlusion (Fig. 8). The dissociation of torque and vertical bracket position makes LightForce an excellent tool for controlling the smile arc.8
4. Because of the inherent accuracy of the 3D-printing process, the slot dimensions are consistently accurate, ensuring effective expression of the custom bracket prescription (Fig. 9).
5. The precise anatomical adaptation of the bracket base to the tooth surface allows optimal bond strength to be achieved with minimal adhesive. This feature is especially appreciable in teeth with significant anatomical variations of the buccal surfaces, such as the first molars (Fig. 10).
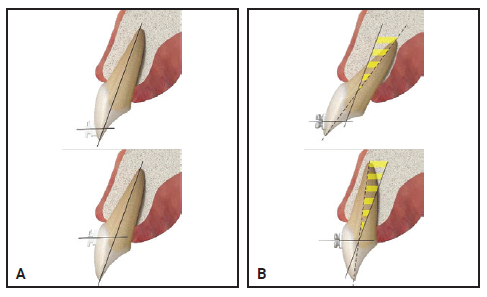
Fig. 8 A. LightForce bracket base adapts to maintain torque, independent of vertical position. B. Same positioning of standard bracket alters torque expression.
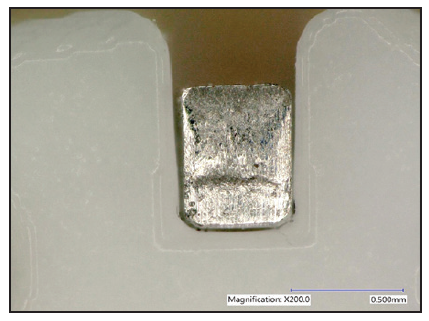
Fig. 9 200× magnification of .019" × .025" stainless steel archwire in .020" LightForce slot. 3D printing ensures parallel slot walls and accurate dimensions.
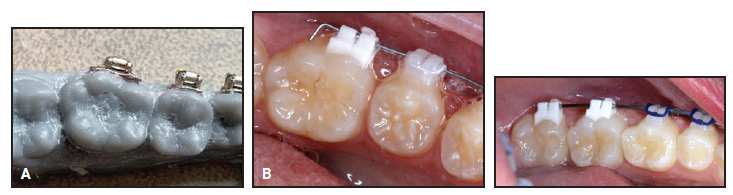
Fig. 10 A. Fit of standard molar tube. B. Two examples of LightForce custom molar tubes.
Case Report
A 13-year-old male presented with the chief complaint of crowding. He had a Class I occlusion with a slightly hyperdivergent skeletal pattern and mild proclination of the lower incisors (Fig. 11, Table 1). Anterior crowding was present in both arches, and the maxillary lateral incisors were palatally displaced. The upper right lateral incisor was in crossbite with the lower right lateral incisor and canine.
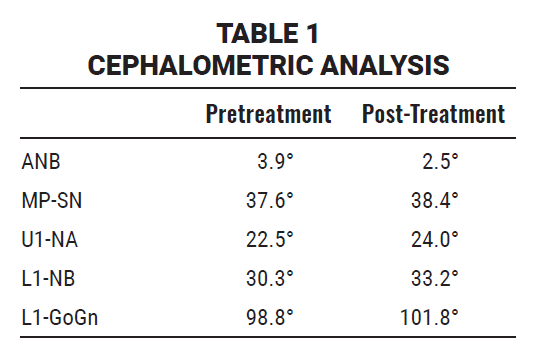
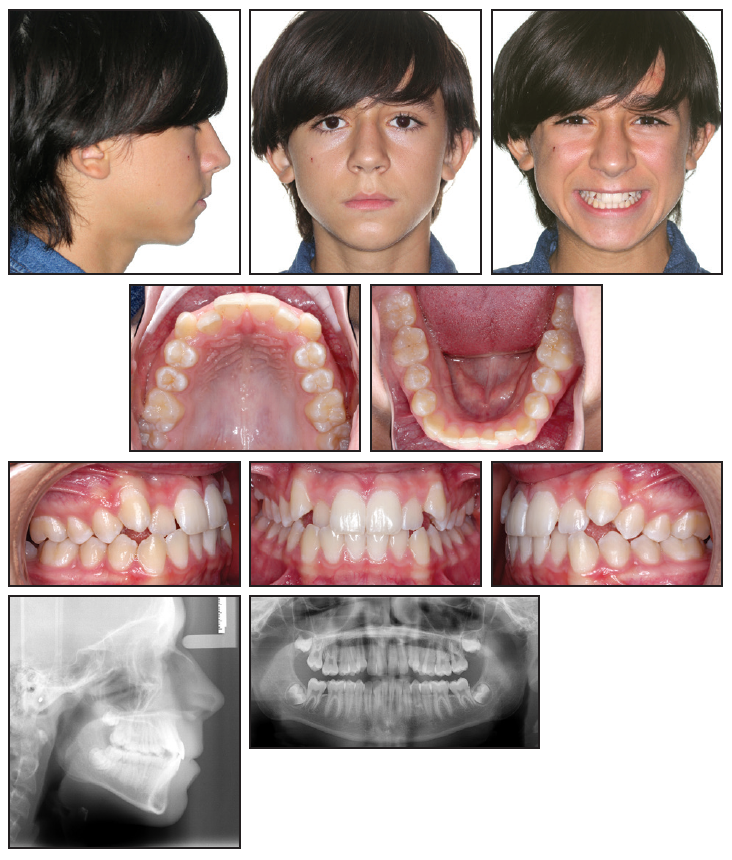
Fig. 11 13-year-old male patient with slightly hyperdivergent skeletal pattern, mild proclination of lower incisors, anterior crowding in both arches, palatally displaced upper lateral incisors, and crossbite of upper right lateral incisor with lower right lateral incisor and canine before treatment.
A nonextraction treatment protocol was planned, despite the clinical challenge of maintaining appropriate torque of the upper- and lower-incisor crowns in the presence of anterior crowding. The .020" LightForce slot size was selected, and the teeth were set up in LightPlan to achieve ideal alignment, a canine-protected occlusion, ideal torque, and an increased overbite (Fig. 12).
Indirect bonding of LightForce brackets from first molar to first molar was completed at the initial visit (Fig. 13). Because this case was treated prior to the availability of LightForce custom second-molar brackets, the second molars were directly bonded with standard brackets at the second visit.
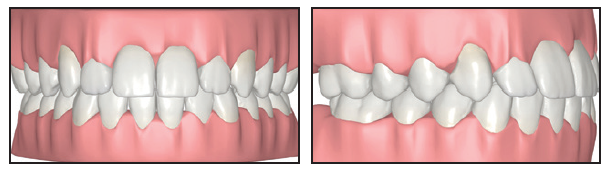
Fig. 12 LightPlan setup for .020" slot size, with goals of ideal alignment, canine-protected occlusion, ideal torque, and increased overbite.
Vertical elastics were worn nightly from the upper canines to the lower canines and first premolars during the first four months of treatment. No bracket repositioning was needed. The final archwires** were upper .019" × .025" nickel titanium and lower .017" × .025" TMA.*** A single step-out bend was added to the final lower wire for detailing of the left lateral incisor.
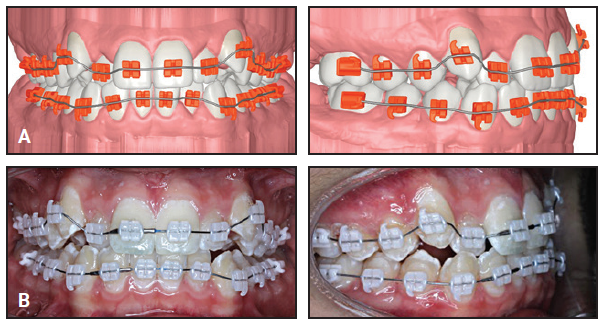
Fig. 13 A. Bracket setup in LightPlan. B. Actual indirect-bonded brackets.
A satisfactory occlusal and esthetic result was achieved in precisely eight months of treatment, involving six scheduled visits and one wire-maintenance visit (Fig. 14).
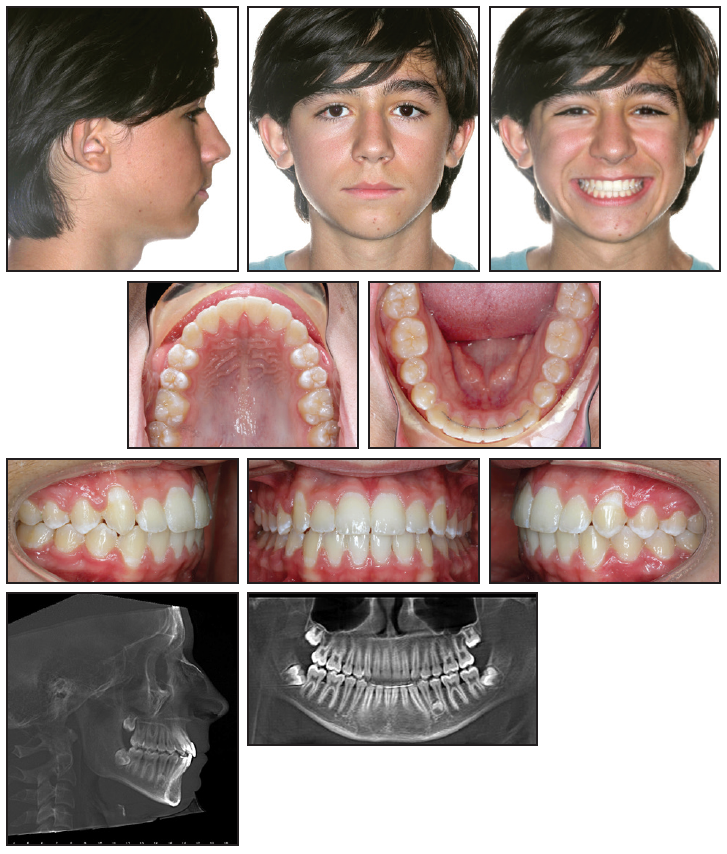
Fig. 14 Patient after eight months of treatment.
Cephalometric analysis confirmed good control of the dentition (Table 1). A slight proclination of the upper and lower incisors was attributable to the initial crowding and nonextraction treatment plan. A supernumerary tooth was detected in the lower left quadrant, and the patient was referred to an oral surgeon for evaluation. Notably, the clinical outcome was strongly correlated with the projected outcome in LightPlan (Fig. 15).
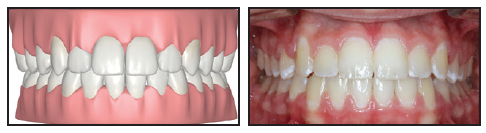
Fig. 15 Strong correlation between outcome predicted in LightPlan and actual treatment result.
Fourteen months after treatment, the results remained stable and the patient continued to display excellent esthetics (Fig. 16). This case thus demonstrates the accuracy of the LightForce system and its ability to harness the latest advances in digital technology to plan and execute individualized orthodontic treatment.
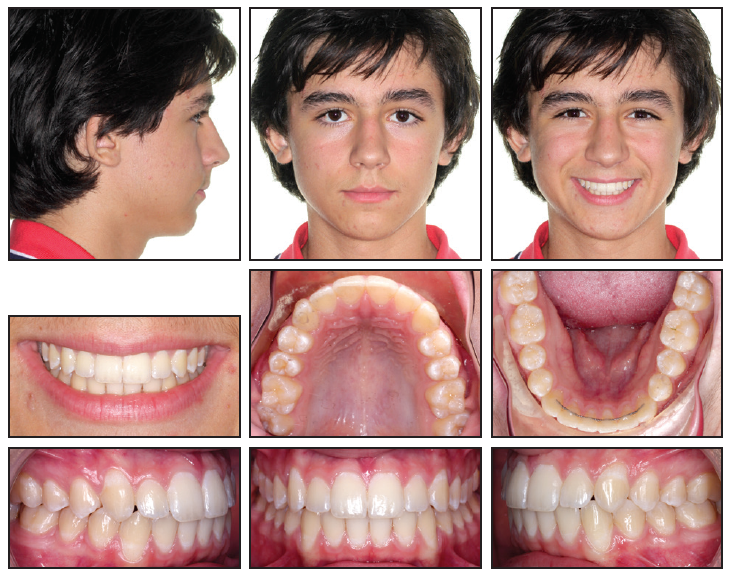
Fig. 16 Patient 14 months after treatment.
Discussion
LightForce 3D-printed fixed appliances represent a major advancement in the evolution of the straightwire appliance. Full customization of labial orthodontic brackets with a complete digital workflow opens new possibilities for treatment planning and clinical case management. This cutting-edge advancement in CAD/CAM fixed appliance technology facilitates precise treatment planning, individualized outcomes, efficient treatment, and optimal treatment results.
(TO BE CONTINUED)
FOOTNOTES
- *LightForce Orthodontics, Burlington, MA; www.lf.co.
- **G&H Wire Company, Franklin, IN; www.ghwire.com.
- ***Trademark of Ormco Corporation, Brea, CA; www.ormco.com.
REFERENCES
- 1. Creekmore, T.D. and Kunik, R.L.: Straight wire: The next generation, Am. J. Orthod. 104:8-20, 1993.
- 2. Weber, D.J. II; Koroluk, L.D.; Phillips, C.; Nguyen, T.; and Proffit, W.R.: Clinical effectiveness and efficiency of customized vs. conventional preadjusted bracket systems, J. Clin. Orthod. 47:261-266, 2013.
- 3. Alford, T.J.; Roberts, W.E.; Hartsfield, J.K. Jr.; Eckert, G.J.; and Snyder, R.J.: Clinical outcomes for patients finished with the SureSmile method compared with conventional fixed orthodontic therapy, Angle Orthod. 81:383-388, 2011.
- 4. Spitz, A.; Gribel, B.F.; and Marassi, C.: CAD/CAM technology for digital indirect bonding, J. Clin. Orthod. 52:621-628, 2018.
- 5. Dawood, A.; Marti Marti, B.; Sauret-Jackson, V.; and Darwood, A.: 3D printing in dentistry, Br. Dent. J. 11:521-529, 2015.
- 6. Tian, Y.; Chen, C.; Xu, X.; Wang, J.; Hou, X.; Li, K.; Lu, X.; Shi, H.; Lee, E.S.; and Jiang, H.B.: A review of 3D printing in dentistry: Technologies, affecting factors, and applications, Scanning, July 17, 2021.
- 7. Waldman, A.; Garvan, C.S.; Yang, J.; and Wheeler, T.T.: Clinical efficiency of LightForce 3D-printed custom brackets, J. Clin. Orthod. 57:274-282, 2023.
- 8. Sarver, D.M.: The importance of incisor positioning in the esthetic smile: The smile arc, Am. J. Orthod. 120:98-111, 2001.
COMMENTS
.